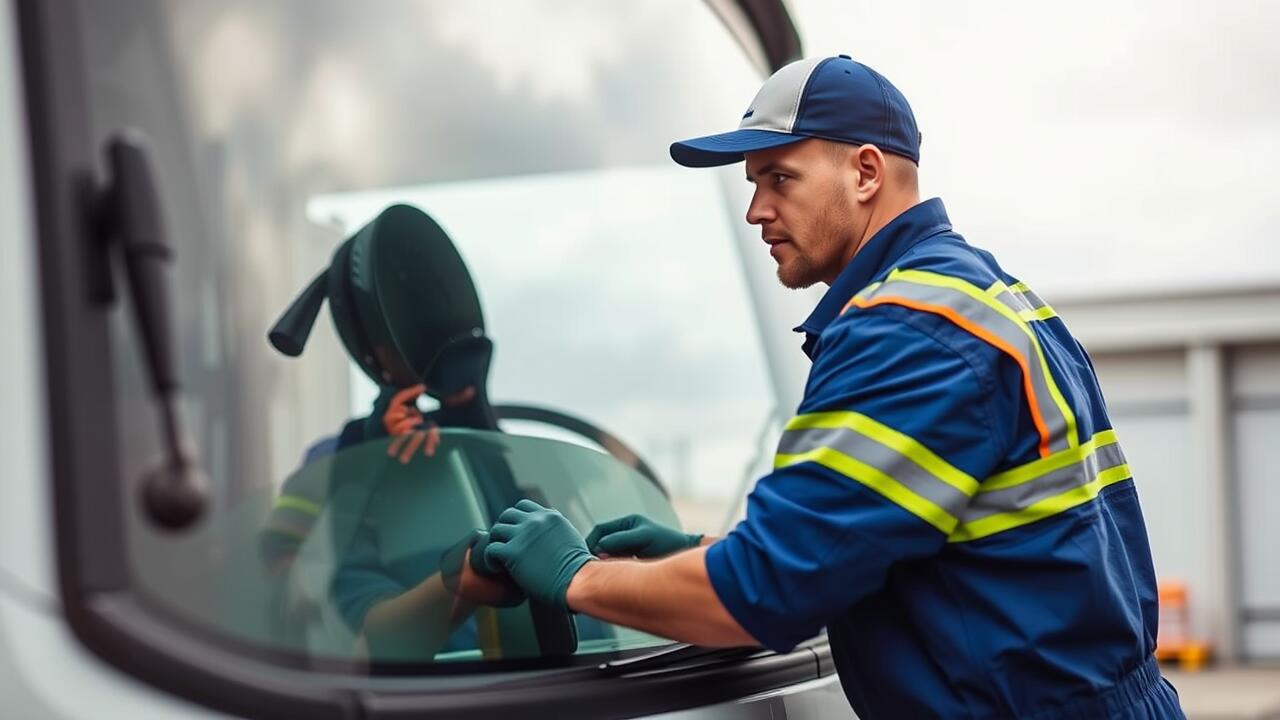
Table Of Contents
Supplier Relationships
The relationships between suppliers play a crucial role in determining wait times for truck windscreen replacements. Suppliers often manage inventory levels and distribution logistics, which impacts how quickly replacement glass can be sourced. Strong partnerships with manufacturers and distributors can lead to better access to stock and timely deliveries, ensuring that the required materials are on hand when needed. A reliable supplier can significantly reduce delays, especially when demand fluctuates or when specific types of windscreens are in high demand due to industry trends or seasonal variations.
Furthermore, the efficiency of the supply chain relies heavily on well-established networks. Disruptions in this network can result in longer wait times, affecting the overall process of truck windscreen replacement. If a supplier faces delays in shipping or has limited inventory on hand, repair businesses may have to wait longer for the necessary parts to arrive. Ultimately, a seamless connection between suppliers and service providers is essential for maintaining prompt turnaround times in truck windscreen replacements.
Importance of Supplier Stock and Logistics
The availability of stock and efficient logistics play a crucial role in the timing of a Truck Windscreen Replacement. When suppliers maintain adequate inventories of commonly used windscreen types, the likelihood of a prompt replacement increases significantly. In contrast, delays can arise when specific windscreens are out of stock or require ordering from distant locations. The overall efficiency of the supply chain can dramatically affect how quickly technicians can access the necessary parts.
Additionally, the logistics involved in the delivery process impact wait times. Reliable transport services and strategically located warehouses facilitate quicker access to truck windscreens. If suppliers can manage their stock effectively and ensure timely deliveries, customers benefit from reduced downtime. This emphasis on supplier stock and logistics is essential for ensuring that Truck Windscreen Replacement services are performed without unnecessary delays.
Technician Availability
The availability of skilled technicians plays a crucial role in determining how quickly truck windscreen replacements can be carried out. A shortage of qualified workers can lead to delays in scheduling appointments for customers. In many regions, the growing demand for professional automotive services has outpaced the number of trained technicians, further complicating the situation. With fewer workers available, companies may struggle to meet the influx of replacement requests, extending wait times beyond the expected range.
Experience also significantly impacts the efficiency of truck windscreen replacements. Skilled technicians possess the expertise to diagnose issues rapidly and complete installations with precision. When there are fewer experienced professionals in the field, the quality of service may decline alongside the wait times. Businesses that invest in training and retaining their workforce can provide more timely replacements, ensuring they can accommodate customer needs promptly while maintaining high standards of service.
The Role of Skilled Labour in Timely Replacements
Skilled labour plays a crucial role in ensuring that truck windscreen replacement is carried out efficiently and effectively. Technicians with specialised training possess the necessary expertise to handle various models and types of trucks. Their experience not only increases the speed of the replacement process but also enhances the quality of the installation, reducing the likelihood of issues such as leaks or improper sealing. A well-trained technician can assess the unique needs of each vehicle and recommend the best course of action.
Furthermore, the availability of skilled workers can significantly impact wait times. In areas where there is a shortage of qualified technicians, businesses may struggle to fulfil replacement requests promptly. High demand for truck windscreen replacements can lead to longer waits if not enough skilled labour is available. Ensuring a steady workforce of skilled labour is essential for maintaining timely and effective service in the truck windscreen replacement industry.
Complexity of the Replacement Process
The complexity of truck windscreen replacement can arise from various factors, significantly affecting wait times. The specific make and model of the truck often dictate the type of windscreen required. Some vehicles may necessitate custom fittings or particular adhesives, leading to longer periods for acquiring the right materials. If the windscreen features advanced technology, such as sensors or heating elements, the replacement process can become even more intricate, requiring technicians with specialised knowledge.
Additionally, the condition of the truck itself can influence the time needed for the replacement. If there are underlying issues, such as corrosion or damage to the frame, additional repairs might be necessary before proceeding with the windscreen installation. This can result in extended wait times, as technicians must ensure that the truck is roadworthy before fitting a new windscreen. Each of these complexities contributes to the variability in the duration of truck windscreen replacement services.
Factors Making Some Replacements More Challenging
Certain truck windscreen replacements are inherently more complex due to the unique design and structure of specific vehicle models. For example, some trucks feature advanced safety systems integrated into the windscreen, such as collision detection or adaptive cruise control. Removing and reinstalling these systems requires specialised skills and knowledge, which can extend the replacement timeline significantly. Additionally, bespoke fittings for certain models may not be readily available, leading to delays as suppliers arrange for the correct parts.
The environmental conditions during the replacement process can also contribute to the challenges associated with truck windscreen replacement. Factors such as extreme temperatures or high humidity can affect the adhesives used and the overall curing process. If the conditions are not optimal, technicians may need to wait for more favourable weather or adjust their methods to ensure the integrity of the installation. This unpredictability can add to the total wait time, as both the technician’s expertise and the external environment play crucial roles in achieving a successful windscreen replacement.
FAQS
Why do wait times for truck windscreen replacements vary so much?
Wait times can vary due to several factors, including supplier relationships, technician availability, and the complexity of the replacement process. Each of these elements can affect how quickly a replacement can be completed.
How do supplier relationships impact wait times?
Strong relationships with suppliers can lead to better stock availability and more efficient logistics, which can shorten wait times. Conversely, if a supplier has limited inventory or logistical issues, it can lead to longer wait times for parts.
What role does technician availability play in the replacement process?
The availability of skilled technicians is crucial for timely replacements. If there are not enough qualified technicians to handle the workload, it can lead to delays in scheduling and completing replacements.
Are all truck windscreen replacements the same in terms of complexity?
No, the complexity of the replacement process can vary significantly depending on factors such as the make and model of the truck, the type of windscreen, and any additional features like sensors or heating elements. More complex replacements typically require more time and expertise.
What can I do to minimise wait times for my truck windscreen replacement?
To minimise wait times, consider scheduling your replacement during off-peak periods, ensuring that you have all necessary information ready (like the truck's make and model), and choosing a service provider with strong supplier relationships and readily available technicians.